Tundish
Tundish applications are critical in the continuous casting process of steelmaking, where tundishes are used to transfer molten metal from the ladle to the mold. Lined with high-performance refractory materials, tundishes ensure smooth, controlled metal flow and help maintain the molten metal’s temperature while removing impurities.
In steel plants, tundish applications improve casting efficiency and metal quality by reducing oxidation and ensuring uniform metal flows into the mold. The refractory linings protect the tundish from extreme heat and chemical wear, enhancing its durability and reducing maintenance costs. Tundish applications play a key role in achieving high-quality steel production and optimizing the continuous casting process.
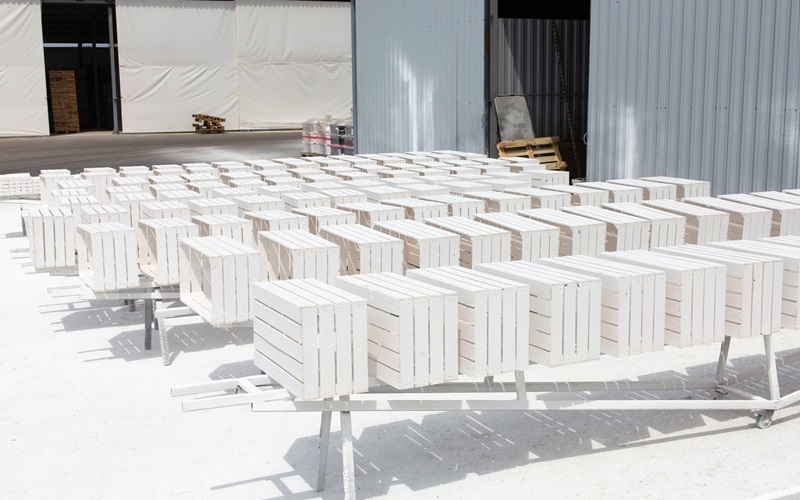
Zirconia Nozzles
Zirconia nozzles are high-performance refractory products used in the continuous casting process to control the flow of molten metal from the tundish to the mold. Made from zirconia-based refractory materials, these nozzles are designed to withstand extreme temperatures, corrosion, and erosion caused by molten steel and slag. Their excellent thermal shock resistance and chemical stability make them ideal for handling high-temperature operations in steelmaking.
Zirconia nozzles ensure precise control over metal flow, improving casting accuracy and the quality of steel products. They are particularly suitable for applications involving high-grade steel, where strict metallurgical control is required. Their durability and resistance to wear reduce maintenance downtime and enhance the overall efficiency and reliability of continuous casting operations, making them a preferred choice in modern steel plants.
Tundish Nozzle
Tundish nozzles are essential refractory components used in the continuous casting process to control the flow of molten metal from the tundish to the mold. Made from high-performance refractory materials like alumina, zirconia, or other specialized compounds, these nozzles are designed to withstand extreme temperatures, corrosion, and erosion. Their primary function is to regulate the flow of metal, ensuring precision and minimizing defects during the casting process.
Tundish nozzles play a crucial role in steelmaking by improving the quality of the cast metal, preventing oxidation, and ensuring uniformity in the metal flow. Their durability and resistance to wear extend the life of tundish equipment, reduce maintenance costs, and enhance overall casting efficiency. By providing accurate control over molten metal distribution, tundish nozzles help in producing high-quality steel products, supporting the smooth operation of continuous casting lines in steel plants.
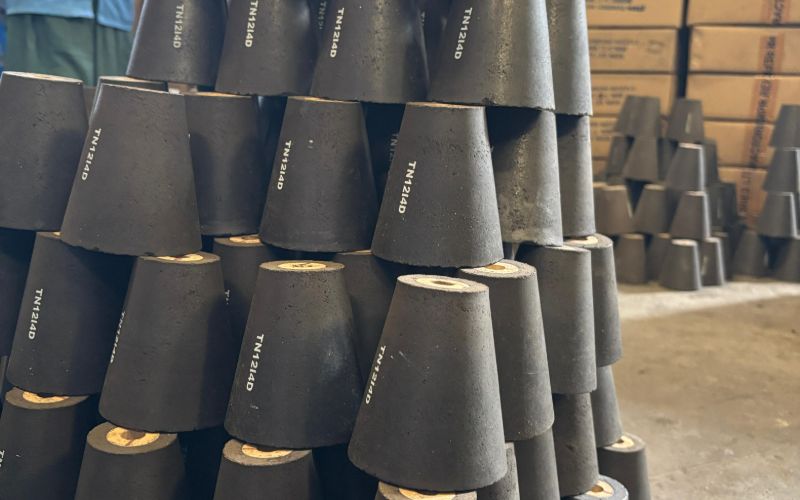
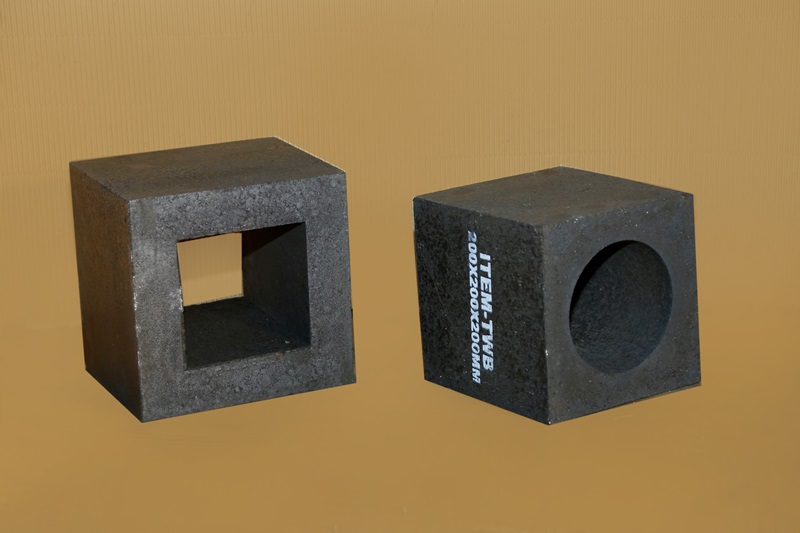
Tundish Well Block
Tundish well blocks are critical refractory components used in the tundish to form and support the well area through which molten metal flows into the casting nozzle. Made from high-grade refractory materials like alumina, magnesia, or zirconia, these blocks are designed to withstand extreme temperatures, mechanical stress, and chemical erosion caused by molten steel and slag. Their robust design ensures the structural integrity and efficiency of the tundish during continuous casting.
These well blocks play a vital role in maintaining smooth metal flow, preventing leaks, and ensuring the quality of the cast metal. Their durability and thermal insulation properties extend the life of tundish components, reduce downtime, and enhance operational efficiency. Tundish well blocks are essential for consistent casting performance in steelmaking, supporting high productivity and superior product quality in demanding industrial environments.
Tundish Board/Tundish Powder
Tundish boards and tundish powders are essential materials used in the continuous casting process to enhance tundish performance and improve steel quality. Tundish boards are disposable refractory linings made from heat-resistant materials, providing thermal insulation and protecting the tundish shell from molten metal damage. They help maintain the molten steel’s temperature and reduce energy losses. Tundish powders, on the other hand, are applied to the molten steel’s surface to prevent oxidation, absorb impurities, and form an insulating layer.
Both products play a crucial role in steelmaking by improving casting efficiency, minimizing metal contamination, and extending tundish life. Tundish boards ensure easy maintenance by simplifying the cleaning and relining process, while tundish powders enhance the quality of molten steel by reducing slag formation and temperature fluctuations. Together, they contribute to consistent and efficient steel production in modern steel plants.
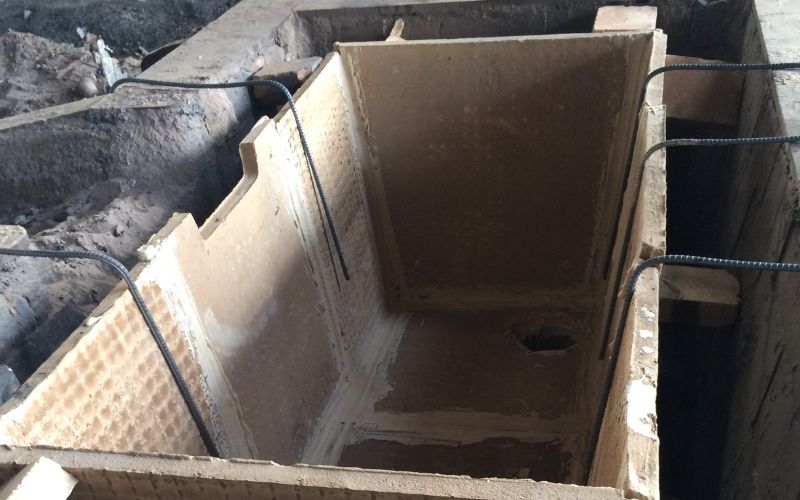
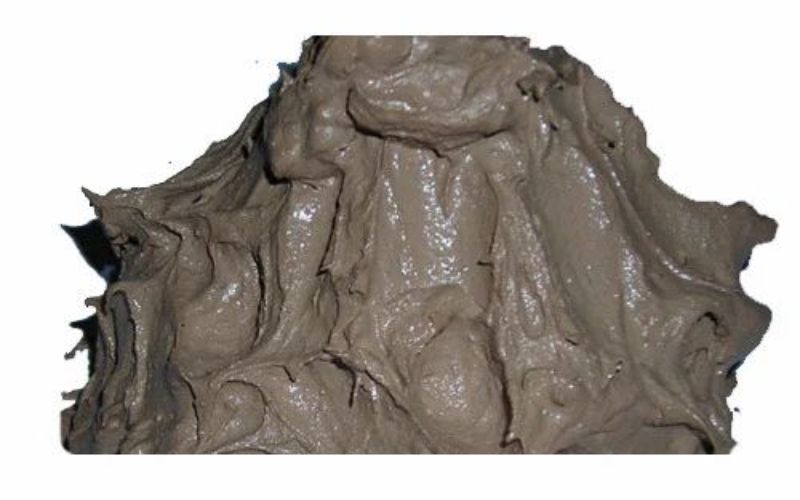
Gar seal
Gar seals are specialized refractory components used in the tundish and other high-temperature industrial applications to prevent leakage and ensure a tight seal between refractory linings and nozzles. Made from high-quality refractory materials like alumina or zirconia, gar seals are designed to withstand extreme temperatures, chemical erosion, and mechanical stresses. They ensure a secure fit, minimizing the risk of molten metal leakage and improving operational safety.
Gar seals play a vital role in maintaining the efficiency of the continuous casting process by ensuring precise metal flow and preventing contamination. Their durability and reliability reduce maintenance requirements, extend the service life of tundish components, and support high-quality steel production. These seals are essential for enhancing the safety, consistency, and productivity of modern steelmaking operations.
Gar Pack
Gar packs are pre-assembled refractory sealing systems used in tundish operations to provide a secure and reliable connection between the tundish nozzle and other refractory components. They are made from high-performance materials like alumina or zirconia, designed to withstand extreme temperatures, chemical corrosion, and mechanical stress. Gar packs ensure a leak-proof seal, preventing molten metal leakage during the continuous casting process.
These sealing systems are essential in steelmaking for maintaining precise metal flow and protecting the tundish and nozzle assembly. Gar packs enhance operational efficiency by reducing downtime, simplifying installation, and extending the service life of critical tundish components. Their durability and performance contribute to consistent casting quality, making them an indispensable part of modern continuous casting systems.
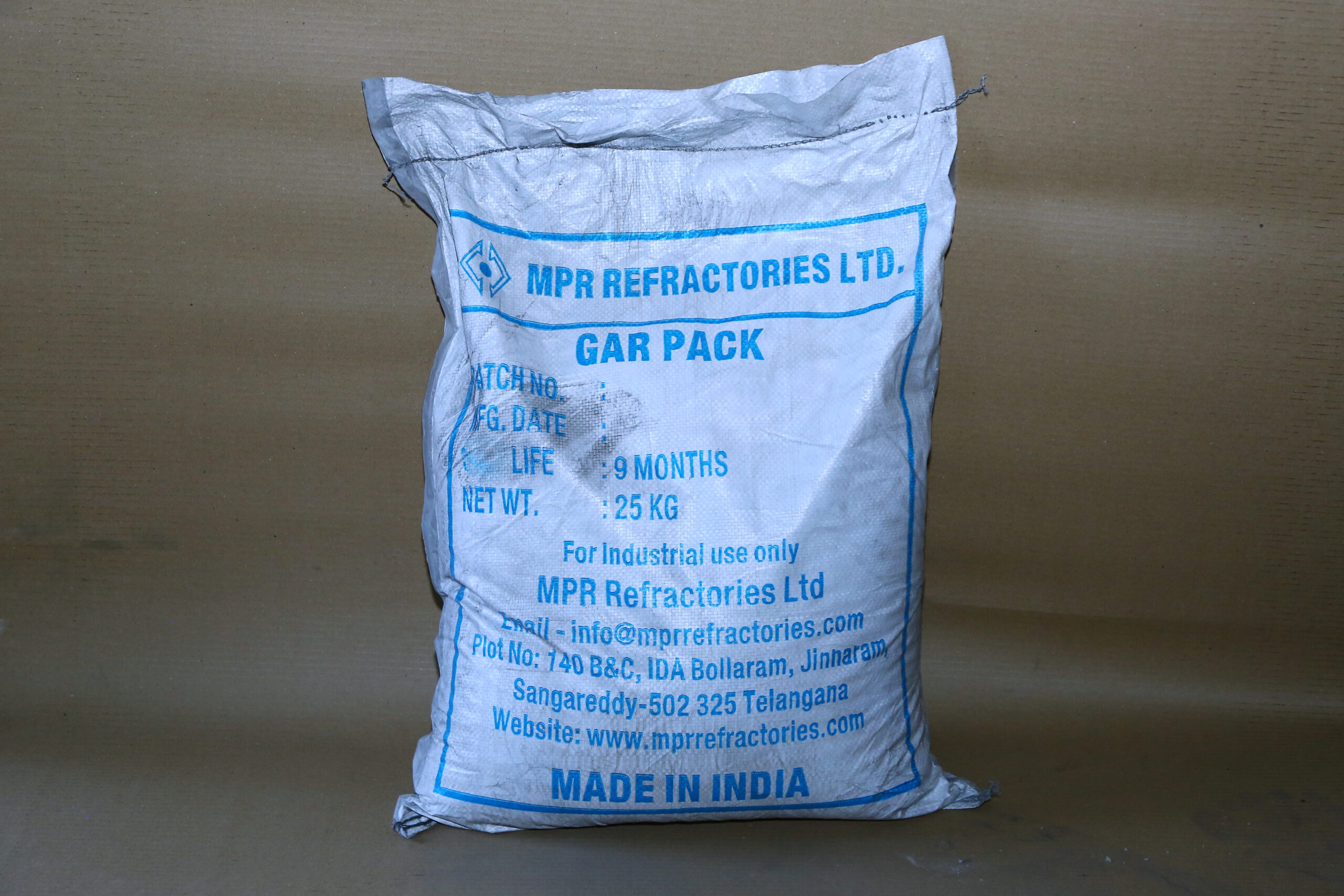
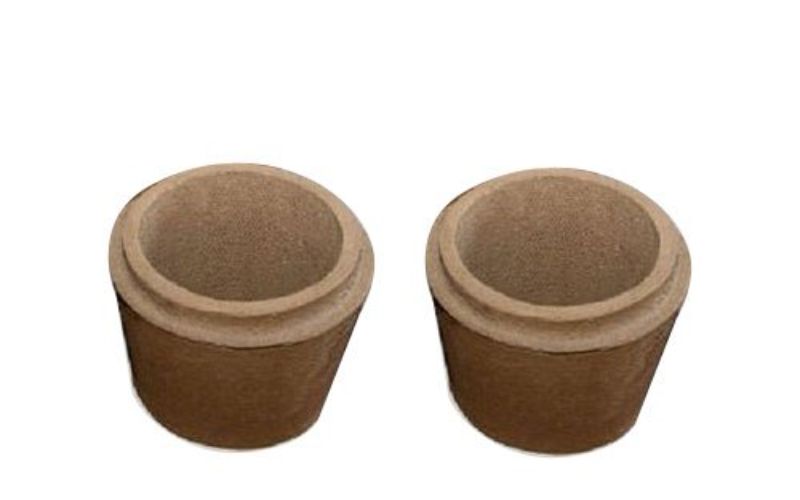
Tundak
Tundak, also known as tundish coating, is a refractory material applied to the inner lining of a tundish in continuous casting operations. Made from high-quality insulating materials, it acts as a protective layer, preventing molten metal from coming into direct contact with the tundish lining. Tundak helps maintain the molten steel’s temperature, reduces thermal losses, and prevents wear and damage to the tundish shell.
Widely used in steelmaking, tundak enhances the efficiency of the casting process by reducing the need for frequent relining and maintenance. Its thermal insulation properties improve energy efficiency, while its ability to minimize contamination ensures high-quality steel production. Tundak plays a vital role in prolonging tundish life, improving operational reliability, and supporting consistent and efficient casting in steel plants.
Bricks
Refractory bricks, commonly known as fire bricks, are specialized building materials designed to withstand high temperatures, mechanical stress, and chemical corrosion. Made from materials like alumina, silica, or magnesia, these bricks offer excellent thermal insulation and stability, making them ideal for lining furnaces, kilns, boilers, and other high-temperature industrial equipment.
Widely used in steel, cement, glass, and petrochemical industries, refractory bricks provide structural strength and protect equipment from extreme heat. Their durability and resistance to thermal shocks help extend the life of industrial systems, ensuring efficient and reliable operations in harsh environments.
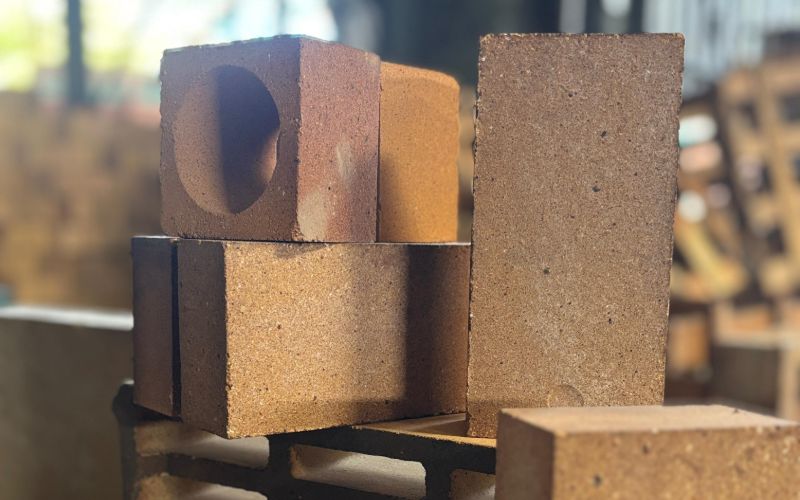